Used within a medical diagnostic application, the custom wire harness pictured here was built by American Precision Assemblers for a medical industry client based in Hoffman Estates, Illinois. Before we could begin assembling this harness, we first needed to gather all appropriate materials and tools. We also clamped in place a layout template, developed in-house, onto a workbench. We then performed a series of manual measurements, which helped us to properly cut, split, and strip the custom 3-pod cable, while additionally stripping any individual wire conductors.
Fulfilling IPC/WHMA-A-620 workmanship standards, we assembled this cable harness using an AMP K-press and Schleuniger wire strippers, along with our in-house template. In order to build this wire harness to meet client specifications, we applied several types of terminals, installed flex-weave per customer print, placed heat shrink tubing over all exposed wires, and assembled grommets on all cable ends. We then inserted all wires into specified connector positions.
After the product was fully assembled, we applied all necessary labels and marked all clamp positions, meeting (+/-) 1/8″ tolerance for precision placement.The finished unit measured 40 feet long with specified breakouts, and featured multi-conductor cables with various wire gauges.
In order to ensure that the cable wire harness met high medical industry standards, we performed a series of in-process visual inspections and measurements. We also completed one final visual inspection and performed an electrical test, which included hi-pot checks. Once assured that the cable harness fulfilled our client’s expectations for quality and performance, we delivered the unit to our customer’s facility in Illinois.
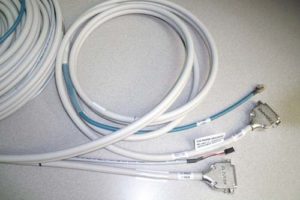
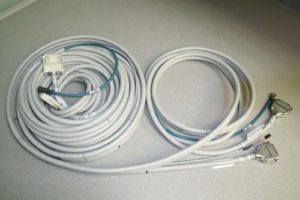