A client in the Automotive industry is using our electronic box build assembly service, along with our other top-notch manufacturing operations. We were able to successfully build this complex component, meeting all customer expectations for quality.
To begin this process, APA first had to purchase sheet metal for the fabrication of the box. Using our drill press and Greenlee punches, we then punched and drilled all necessary holes into the fixture per our customer’s specifications. We then used our Komax wire processing machinery to cut and strip all wiring. We also employed our AMP K-Press to perform all terminal crimping necessary to successfully terminate each connector. After soldering all necessary parts onto the testing fixture, we then attached all wires and connectors and installed all other components, based on our client’s schematic.
This complex testing fixture measured 12X14X6 inches and weighed approximately four pounds. This fixture was equipped with LED lights, conventional lamps, 2 and 3 position switches, a rotary switch, and banana jacks with shorting adapters. To ensure the product met all client requirements, we performed in-process and final visual inspections. We carried out a series of electrical tests using Cirrus testers. We also used a parent/child list to ensure the part lived up to client expectations.
Once assured that the unit met all customer requirements, we then shipped the part out to our client’s facility located in Auburn Hills, Michigan. This custom testing fixture successfully fulfilled all of our client’s product specifications and met IPC-WHMA-A-620 standards for quality workmanship.
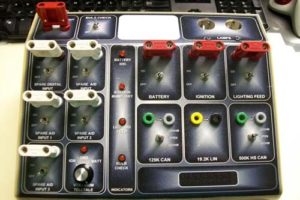
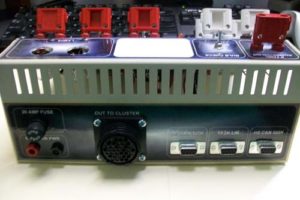